Total Precast
Lofts on Grove
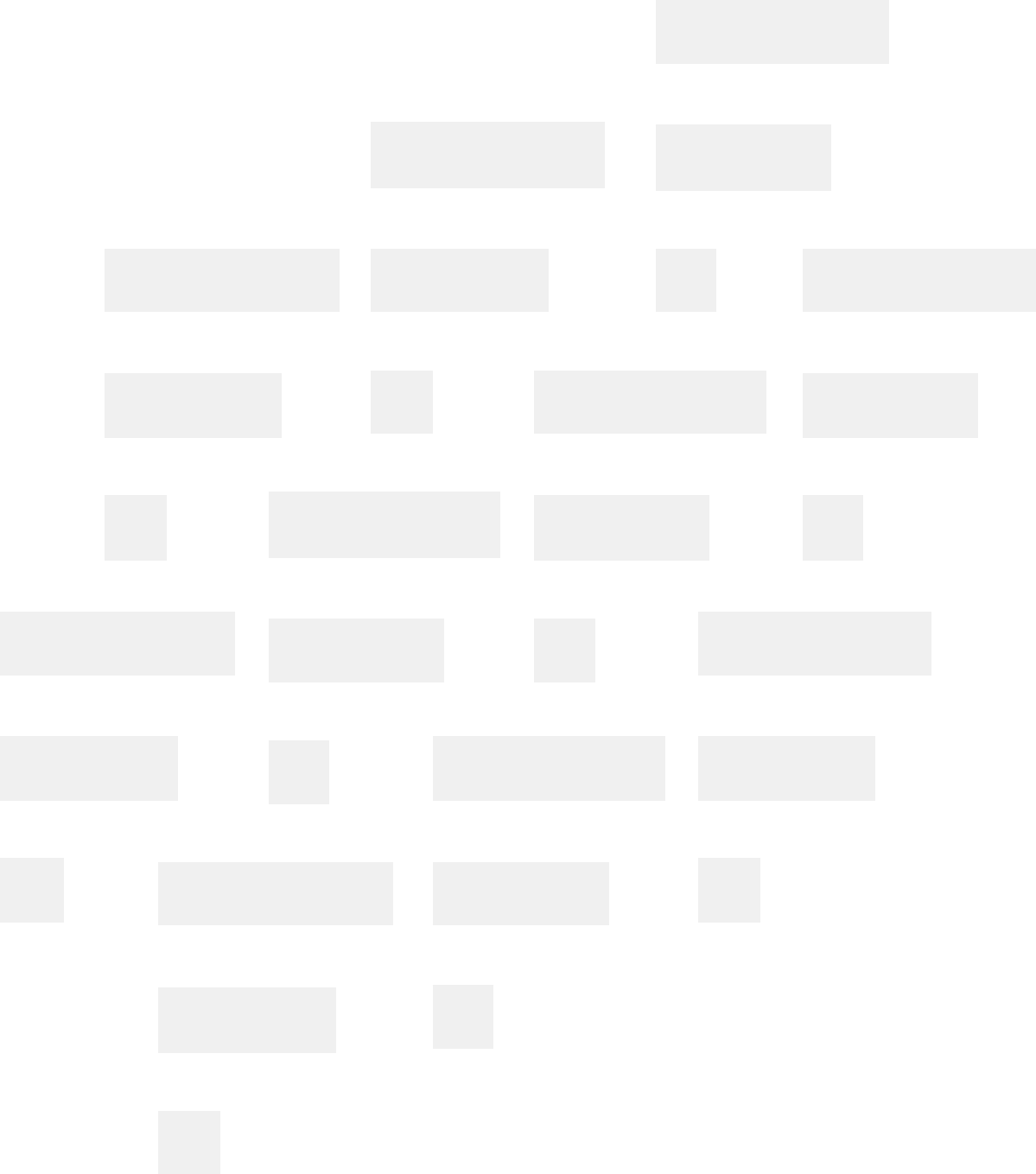
Overview
Lofts on Grove is a 110-unit apartment building in Grand Rapids, Michigan, with retail stores on the main floor, which replaces two dilapidated vacant buildings with much-needed housing. Fabcon joined the project with the goal of developing a total precast system approach using Building Automated Modeling (BIM) to improve thermal performance, safety, and security, plus storm and fire resistance while increasing open space and offering aesthetic versatility.
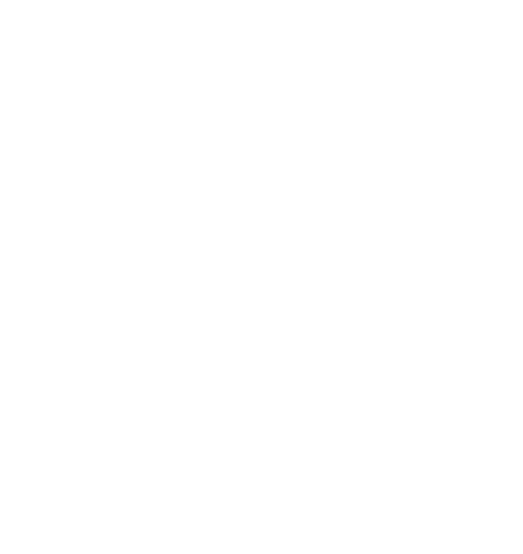
2025 PCI Best Multi-Family Building
Project Details:
General Contractor
First Companies
Engineer of Record
JDH Structural Engineering
Architect
Lott3Metz Architecture, LLC
Fabcon’s Lofts on Grove Apartment Building Project Is Like a Tetris Game with its Residents the Winners
Fabcon’s involvement in developing the 110-unit apartment building in Grand Rapids, Michigan helped minimize potential structural damage, while reducing potential support, upkeep, and insurance costs for the owner and tenants. The accelerated construction timeline and resilient design also helped reduce long-term life-cycle costs while increasing the materials’ service life and durability.
Problem
The new structure, to be built on a brownfield site which once housed two existing structures, required installing the precast around utilities configured to the original site layout, presenting an installation and design challenge. The project owner and design team didn’t want exposed bearing haunches to the hollowcore visible to the residents, which restricted the walls to an eight-inch solid with a dual-bearing hollowcore. Given these and other site logistical restraints and the interior bearing walls’ configuration, the building had to be towered up in the northernmost end for the first bay, then stair stepped for the remainder of the way.
The main floor retail space, on the structure’s South side facing downtown Grand Rapids, presented another challenge as it needed to be completely open while supporting the three upper floors. This necessitated Fabcon designing and pouring a precast “wall beam” that comprised the second floor’s full height, allowing the framing to avoid having a beam system exposed in the retail space, while maximizing its heights.
Yet the exterior architectural features presented the largest challenge, with a design requiring that liner, thin brick and reveals be incorporated into the panels to match existing features of the area and accommodate a neighborhood planning commission request.
Solution
The project consisted of 82,300 square feet (nearly 600 pieces) of 12-inch hollowcore plank spanning two units, allowing the space to be reconfigured more easily in the future by creating larger spaces between the eight-inch bearing walls.
Fabcon used precast to provide a durable, abuse resistant, rated wall assembly for this owner-operated leased building. The use of precast interior bearing walls, and egress walls provided a structural system that could withstand wear and tear over an extended period without the need to repair or replace in between tenants. Precast also provided an exterior that needed minimal maintenance and could tolerate the high traffic area, minimizing the risk of major repairs due to possible vehicle impact, foot traffic, or de-icing salts.
The Fabcon team incorporated multiple detailing and fabrication methods and intricately coordinated brick models, utilizing ¾” thin brick on the first-floor exterior panels and several lobby interior panels, and using a brick liner with reveals that would be painted for the rest of the interior. The panels also required multiple rubber master molds with minimal repetition, prompting the Fabcon team to use fixed mini rubber liners on plywood backing cut to fit specific panel positions. This created a puzzle-type formatting system allowing the pieces to be used across multiple panel types, yet in specific positions. This forming method was very much like a Tetris game, where cut segments were moved over a few spaces to create a unique feature with an individual panel.
Results
The forming method offered a creative solution that saved plant labor, casting time, and materials, while using fire-resistant materials for the construction contributed to a significantly reduced permitting timeline.
Part of a highly capable BIM team, Fabcon coordinated the Mechanical, Electrical, and Plumbing (MEP) trades without consuming substantial amounts of the architectural team’s time. Fabcon also provided a substantial benefit with a clean on-site construction process that was aligned with the project schedule. The combined fabrication, design, and form liner team arrived at a solution that led to the requested architectural features without impacting the price or schedule.
”With all aspects of the building, the exterior, the roof, the stair systems, the floor plates, and a lot of finished walls within the building being concrete, the sustainability and resiliency to damage/failure is very high! You can’t beat concrete for a finished product surface!
Josh Reynolds, CDTSenior Project Manager | First Companies
Related Projects